Choosing the Right Blow Molding Process for Your Bottle
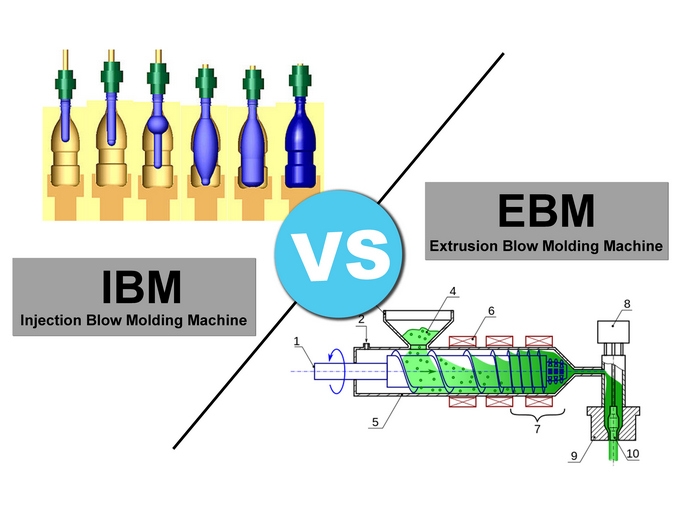
Selecting the appropriate blow molding process for your bottle is a crucial decision that significantly impacts its quality and functionality. In the realm of blow molding, there are three primary types: Extrusion Blow Molding (EBM), Injection Blow Molding (IBM), and Two-Stage PET Stretch Blow Molding (ISBM). Each method offers distinct advantages based on specific requirements.
Extrusion Blow Molding (EBM)
Extrusion Blow Molding stands as the fundamental technique in blow molding. This process involves melting plastic resin and forming it into a parison, which is then expanded into the mold. In comparison to injection blow molding, extrusion can manufacture larger components and is cost-effective due to minimal internal tensions in the part. However, it tends to generate more waste and provides less control over essential dimensions. Extrusion blow molding can be run as a continuous or semi-continuous process based on the application's demands.
Injection Blow Molding (IBM)
In the injection blow molding process, the plastic preform is injected and then transferred to the blow mold station via a rod. The preform takes its shape and is molded by air pressure in accordance with the design of the female blow mold. Injection blow molding is ideal for producing bottles with precise neck finishes and intricate designs. It suits small to medium production volumes and is advantageous for products requiring a high level of precision. Various bottles, especially for cosmetics, lotions, and personal care items, are commonly produced using this method.
Two-Stage Injection Stretch Blow Molding (ISBM)
Two-stage injection stretch blow molding involves two machines: the injection molding machine and the stretch blow molding machine. Initially, plastic is molded into a fully-cooled preform in the first machine, which is then sent to the second machine. The preform usually includes the neck and thread of the bottle, and it can be sold to a third party even before it is blown using the second machine. When received by the latter, they are then unscrambled, reheated using infrared radiation, and conditioned before molding.
By using this two-stage approach, shipping costs can be reduced by shipping preforms instead of empty bottles to a bottling plant. The bottles are blown at the plant prior to filling, resulting in increased output volume, making it ideal for industries requiring a high quantity of rapidly produced bottles, such as the food packaging and cosmetics industries.
For instance, the 5-gallon PET drum exemplifies cost-saving through shipping preforms instead of empty bottles. The CMS-Q1 series PET fully electric stretch blow molding machine is an excellent choice for producing 5-gallon water tanks, whether they are for one-time use or reusable bottles.
In conclusion, your decision between EBM, IBM, or ISBM should be guided by factors like design complexity, production volume, and cost considerations. Thoroughly evaluate your bottle's specifications to determine the most suitable blow molding process that aligns with your needs, ensuring optimal results and overall satisfaction. For further information or inquiries, please provide your contact information or reach out to Chia Ming via email.